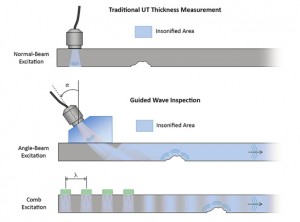
Ultrasonic guided waves have generated growing interest over the past decade as the range of applications for which guided waves are proving useful is rapidly growing. The nature of guided waves, which can propagate long distances, yields tremendous potential for time and cost savings during the inspection of a wide variety of structures from railway tracks to pipelines to aircraft skins. Guided waves can achieve much greater inspection ranges than conventional ultrasonic testing methods because they utilize the structure itself as a waveguide by exploiting resonances between the boundaries of the structure (e.g. the surfaces of a plate or the OD and ID of a pipe). Therefore, while conventional “bulk” wave UT systems can generally only inspect an area very close to or directly beneath the transducer, guided wave systems can detect flaws many feet away from the transducer, and in some cases several hundred feet away. Due to the unique properties of guided waves, they are also capable of detecting small defects at very low frequencies compared to traditional UT. this capability increases penetration power.
The benefits of guided waves can include:
- 100% coverage throughout the thickness of the structure
- Inspection over long distances from a single probe position
- Ability to inspect hidden and inaccessible regions of structures as well as structures under water, coatings, insulation, and concrete
- Beam focusing capability for improved probability of detection and inspection confidence, reduced false alarm rate, and improved defect resolution and scan coverage
- Cost effectiveness because of inspection simplicity and speed
- Avoidance of removal/reinstatement of insulation or coatings, except at location of transducer tool

Along with the greater potential that guided waves offer comes an increased level of complexity that challenged researchers and technicians for many years. For instance, while only two wave modes exist for bulk waves in most materials (longitudinal and shear waves), hundreds of guided wave modes may exist in a particular structure. Additionally, guided wave velocities change with the mode and frequency used, and these velocity relationships depend not only on the material of the structure but also on its geometry (e.g. the thickness of the plate or the diameter and schedule of the pipe). However, improvements in computational power, signal processing algorithms, and the understanding of guided wave mechanics have led to great advances in sensor, system, and software design. Complex dispersion curve solutions, focusing algorithms, and signal processing are now handled automatically by the system software to allow the user to successfully complete an inspection without a deep knowledge of the guided wave mechanics at work. The experts at Guidedwave have helped bring ultrasonic guided wave technology into the realm of practical inspection systems.
Guidedwave offers a wide variety of technologies for guided wave inspection of plates/shells, pipes, tubes, storage tanks, and many other structures. Explore the other Knowledge and Product sections to learn more, or contact a Guidedwave engineer.
